Know about the important types of plastic molding such as injection molding, blow molding, compression molding and rotational molding which often utilize plastic resin . Study the applications, benefits and the selection of the appropriate approach to your production demands.

The world of manufacturing may have been changed with the advent of plastic molding in so many different industries, including automotive, aerospace, consumer, and medical devices. To manufacturers, designers of products and any other business with a desire to streamline its production line, it is important to understand the differences between the types of plastic molds. This is the complete handbook that looks into the most relevant molding techniques, the usage, and even the ways to identify the best technique that suits your particular interests.
What is Plastic Molding and Why Does It Matter?
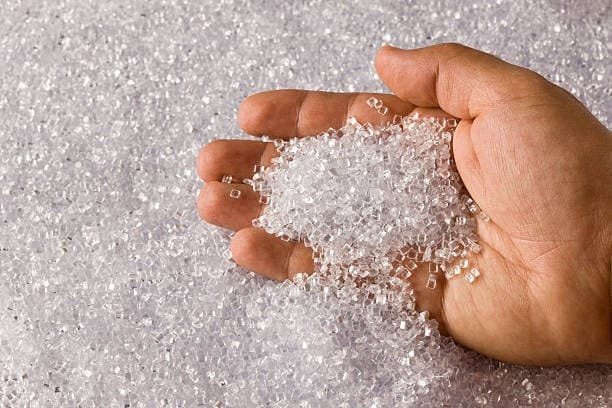
Plastic molding process involves the manufacturing of a piece of plastic into a desired shape through the application of heat, pressure and also specialised moulds. This makes it possible to produce plastic parts of high volume and quality in a relatively low cost by using heated plastic material . The plastic molding is such a versatile product that it cannot be ignored in modern manufacturing as it offers complex shapes, accurate tolerances, and the ease of manufacturing in several cycles that other methods of manufacturing lack.
Plastic molding is much more than another cost savings tool. It makes it possible to realize lightweight design solutions and minimize material waste and favor sustainable manufacturing by using recyclable materials and energy-friendly procedures, making the process cost effective .
Injection Molding: The Most Versatile Manufacturing Method

The most common type of plastic molding is the injection molding process, which constitutes more than 80 percent of all the plastic manufacturing processes. The process entails the high production pressure in which molten plastic material is injected into mould cavity which is closed. Starting with measuring plastic pellets placed in a barrel and heated to reach a molten condition after which the molten plastic is forced by a nozzle system into the mold.
Injection molding is versatile and so the parts can include small electronic components, as well as automotive panels. It is able to mold complex parts or structures such as threads, undercuts and complex surface line work in one process; it is therefore ideal when doing a large production run. Advanced plastic injection molding machines have shortened their cycle to few seconds in the process of creating small parts, and this makes them exceptionally productive.
Quality Management In injection molding quality management is measured by precise temperature, pressure and timing means, ensuring uniform wall thickness part dimensions and properties are predictable throughout a long production run.
Blow Molding: Creating Hollow Plastic Products
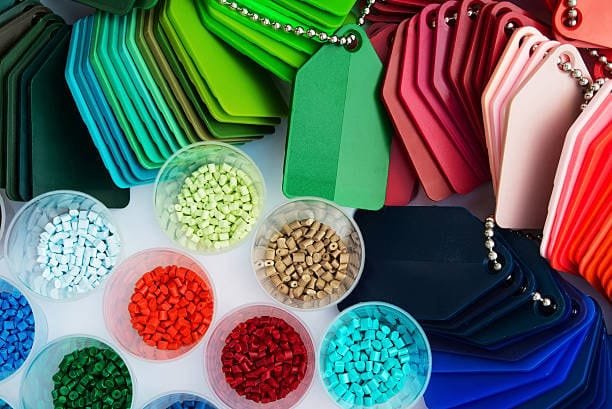
Blow molding has expertise producing hollow plastic wares through inflating hot plastic medium against the inner surface of a mold. This procedure exists in three primary alternatives; there are the extrusion blow molding, injection blow molding and stretch blow molding, all using a heated mold . All the variations have certain benefits in accordance to the product demands and manufacturing quantities.
The top-up production starts by producing a parison (long hollow piece of plastic) or preform followed by inserting it in a forge and inflating it with compressed air. The pliable material stretchs to adopt the form of mold cavity resulting in hollow products that have uniform thickness of the walls and smooth finish on their surface.
The Blow molding process is very effective in making plastic bottles, containers, tanks, etc. which have very good strength to weight ratio. It is quite effective especially when dealing with products with massive requirements and is able to handle a range of plastic materials like polyethylene, polypropylene, and PET.
Compression Molding: High-Strength Applications
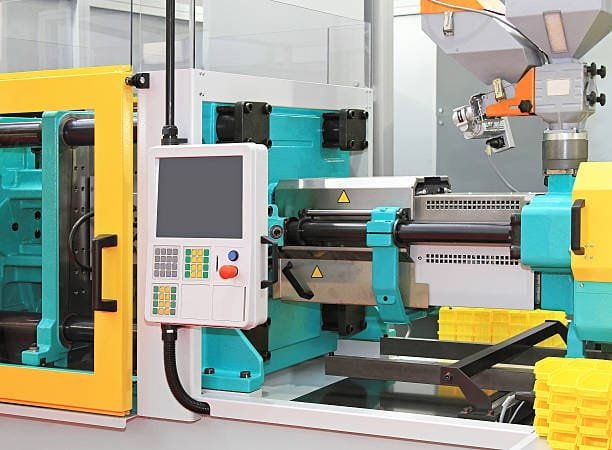
Compression Molding In this molding method, a precise quantity of plastic material is inserted into a vacant mold cavity, the material is then heated and pressurized until it is shaped to match the mold. This method is specially suited to thermoset plastic that becomes hard forever because of the heat and pressure applied in a metal mold .
It has a superior material to waste ratio, thus it is economical in medium to high volume production. Compression molding gives a good surface finish quality and dimensional accuracy of parts, which makes it ideal when parts are to be used structurally where high strength and durability is needed.
They have used automotive components, electrical elements and industrial equipment where mechanical properties and heat resistance are of importance. The procedure additionally allows reinforced plastics made with fiber additions to have additional strength attributes.
Rotational Molding: Large, Seamless Products

Rotational molding or rotomolding is a plastic manufacturing process that involves subjecting a hollow container (often a mold of some kind) to heat, and causing it to rotate about two mutually perpendicular axes. The constant forming of the inside surface of the mold is unique in that the plastic is able to cover the full inside surface of the mold such that the resulting product will have no weld line or stress points.
The steps involved are feeding the plastic powder into a hollow mold and heating in it with a slow rotation. The plastic melts and sticks on the walls of the mold; this forms even thickness on the walls of the part. The final product is detached out of the mold after it is cooled.
Rotational molding is good at large containers, tanks, playground equipment and car parts. The process is flexible in design of complicated shapes and undulating wall thicknesses in the same part, and is therefore good in providing custom applications.
Thermoforming: Sheet Plastic Shaping
Thermoforming manipulates sheets of hot plastic with the aid of vacuum, pressure or a mechanical force to give them a three dimensional form. This is carried out by first (obtaining a clean plastic sheet) placing it in a heating oven until it reaches its forming temperature, after which a mold is forced into it to take a desired form.
The process involves two forms of procedure; the simpler shapes mainly involve vacuum forming whereas the more complicated shapes which are detailed involve pressure forming. Thermoforming is good also in surface reproduction and has the ability to make parts with different wall thicknesses as well as allowing complex undercuts.
Examples are packaging, automotive interior parts, and housing of medical devices and consumer products. It is especially economical to mass production intermediate numbers and prototyping uses.
Extrusion Molding: Continuous Profile Production
The extrusion molding process makes continuous profiles out of a shaped die. It entails heating the plastic pellets to a barrel, which has a rotating screw, which forces the material in the die hole. Then extruded profile is cooled down and cut to specific lengths.
This process renders consistent cross-sectional creations such as pipes, profiles, sheets, and tubes of the same size and material qualities. Extrusion has great rates of production and low wastage of materials and therefore it is very suitable to high volume applications.
Multi-layer products with a dissimilar material property in each layer can be fabricated through a co-extrusion which widens design potentials to more specialized uses that need a defined performance property.
Transfer Molding: Precision Thermoset Processing
Transfer molding borrows some aspects of compression molding and injection molding to carry out thermoset materials with a higher level of precision. It is a manufacturing process in which it transfers pre-measured plastic material in a pot into the cavity of the mold by way of the runner system which is under pressure.
This technique has greater control of material flow and filling the cavity than compression molding thereby leading to much improved part quality and less waste of material. Transfer molding can accept an intricate part geometry including close tolerance as well as high level surface finish.
Its uses are on electronic component, automotive and industrial equipment where accuracy in dimensions and homogeneity of material are vital needs.
Insert Molding: Combining Materials in One Process
Insert molding involves designing or incorporating metal or other material into plastic plastic parts, when molding. Inserting a pre-formed insert in the mold cavity prior to injecting plastic forms an everlasting unification amidst the insert and the plastic material.
Through this process, the secondary assembly operations are eliminated and this cuts the costs and enhances the reliability of the finished product since the possible cause of failure is eliminated. Various inserts also can be used in insert molding with metals, ceramics and other plastics meeting the need.
Typical uses are automotive parts, electrical connections, and medical products where a metal screw, contact, or structural part have to be assembled with a plastic housing.
Overmolding: Multi-Material Product Creation
Multi-material production via overmolding is molding multiple materials together in a single pass or sequentially. In this method one component has a combination of materials, e.g. a rigid plastic surface and a soft rubber grip or seal.
The process is very sensitive in selecting materials used and therefore has to make sure that adhesion of the layers is done properly and also that the materials have similar processing temperatures. Overmolding eradicates assembly functions and offers better functionality and beauty.
Tool handles, electronic appliance housings, automobile interior part, medical equipment where many properties are needed in one part are examples of its applications.
Gas-Assisted Injection Molding: Hollow Structures with Solid Walls
Gas-assisted injection molding In gas-assisted injection molding hollow areas are created within solid injection molded plastic material by injecting inert gas into the mold. The process involves minimal use of materials, no sink marks and parts that have strength to weight ratios.
It consists of partial injection of plastic material where after the viscosity is increased with the injection of gas, leaving the holey или cavities in the piece. Part shape is retained in cooling by the gas pressure eliminating defects characteristic of thick-walled plastic parts.
The advantages are less production cycle, high part quality, and better design freedom of complex shapes. The use areas are automobile parts, furniture and fixtures, parts of appliances that need light weight, but still have structural capabilities.
Foam Molding: Lightweight, Insulated Products
Foam molding creates cellular plastic elements with low weight in that blowing valves are applied in the procedure of molding. The expanding foam leaves internal voids and that lowers weight but does not lose structure.
Structural foams injection molding results in solid skin and foam part with good strength to weight and dimensional stability. Large sections of thick cross-sections can be accommodated and the usages of material and cycle times are reduced.
They can be used in automotive parts, furniture and packaging where light weight and insulation characters becomes a key design factor.
Choosing the Right Plastic Molding Type for Your Project
The type of plastic molding to use is based on several factors such as the part geometry, material requirement, the volume of production and costs among others. Unglazed hollow products are usually best applied on blow molding whereas injection molding is well suited on custom plastic parts that are highly demanding.
The volume of production is one of the factors that plays a major role in determining the process to be used as high capacities are used in injection molding and medium in thermoforming glass blowing other molding processes. The property of the material is also significant and thermosets are to be applied with compression or transfer moulding but thermoplastics are best used with injection or blow moulding.
The cost should involve such items like tooling cost, material costs, cycle times, and secondary operations. Long term production planning allows better justification of using more expensive tooling on a process that will produce lower per part costs on a large production run liquid or pliable material.
Conclusion
Recognizing the types of plastic molding is a vital addition in the process of successful product development and optimization of its manufacturing process. All the molding techniques present their own distinctive features and uses, such as the versatility of injection molding; how rotational molding allows a seamless fabrication of large parts, and so on. The secret of success is to apply the most suitable process to your individual needs with such criteria as the complexity of the parts, the volume of production you need, the qualities of the material and the budget you have. With reasonable consideration and input by competent molding specialists, manufacturers should be able to come up with the best of results with quality achieved and cost kept in check.
About GWT Worldwide
Shenzhen Guanwutong International Freight Forwarding Co., Ltd. ( ГЇ pro ArteEUixon contains “GWT Worldwide” is a professional logistics service operator specialized in global freight forwarding service, global supply chain solution, global e-commerce logistics. Our main services would be air freight and sea freight, China to Europe railway services, international express and courier services, customs clearance and warehousing and Amazon FBA shipping services and labels. Our company is efficient, transparent and customer satisfaction-oriented, because we become your reliable logistic partner to importers/exporters of any size to conduct speedy global trade.