Modern manufacturing depends much on die casting dies since they guarantee the exact shaping of metal parts. Knowing the structure, design, and maintenance of die casting dies becomes crucial as sectors keep needing premium, accurate, and durable die casting parts throughout manufacturing process. This thorough guide will explore die casting die specifics including types, materials, design process, maintenance techniques, and industry uses.
What Are Die Casting Dies?
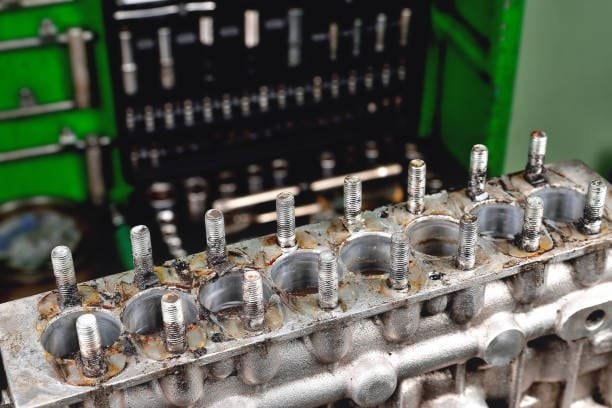
In the die casting process, die casting dies—precision-engineered molds—help to shape molten metal into specified forms complex shapes. These dies are made from robust materials meant to resist high pressures and extreme temperatures and injection techniques. Die casting dies are essential for manufacturers creating intricate, high- volume parts with low error rates.
Importance of Die Casting Dies
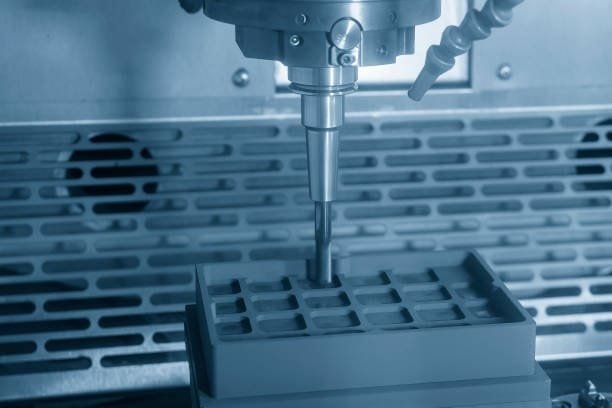
In sectors including automotive, aerospace, electronics, and construction, die casting dies are vital. Important advantages of die casting industry are:
- Improved precision guarantees that components satisfy exact requirements.
- Reduced waste helps to enable mass production, so promoting efficiency.
- Enhanced strength helps to produce sturdy metal parts.
Types of Die Casting Dies
Knowing the several kinds of die casting dies facilitates the choice of the suitable tool for particular manufacturing process needs. The principal forms are:
1. Single-Cavity Dies
- Made to generate one part every injection cycle.
- Perfect for big, detailed components or parts needing exacting detailing.
2. Multiple-Cavity Dies
- Armed with several cavities to generate identical parts concurrently.
- Often used in high-volume production to raise effectiveness.
3. Combination Dies
- Made to create several parts from the same die.
- Often used for building later assembled complementary sections.
4. Unit Dies
- Small-volume manufacturing or specialized designs call for compact, interchangeable dies.
- offers a reasonably priced answer for speciality projects.
5. Family Dies
- Made to generate several connected components in one injection cycle.
- lowers tooling costs and raises general production effectiveness.
Types of Die Casting
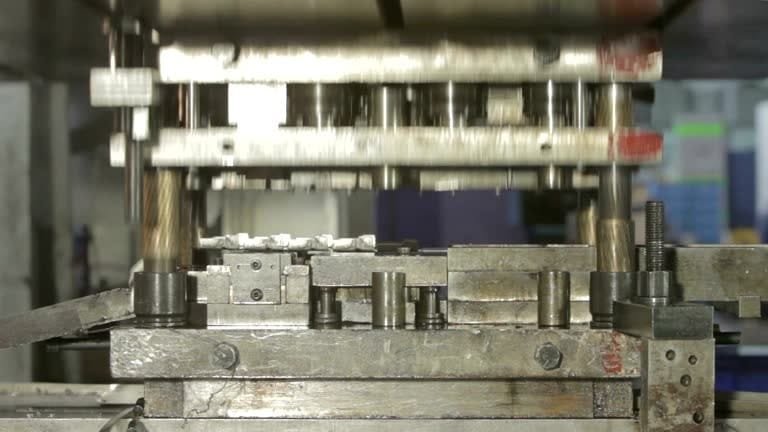
Die casting techniques can be modified depending on the process criteria and the intended qualities of the last product. Two especially important die casting techniques among the several ones used are: zinc die casting, hot chamber die casting and cold chamber die casting. Knowing these techniques will enable one to decide on the best approach for particular uses.
Hot Chamber Die Casting

A “hot chamber” is an internal furnace built right into the casting machine itself. Via a feeding system for aluminum casting, called the “gooseneck,” this furnace is coupled to the die cavity.
Hot chamber die casting is well-known for its fast cycle times of roughly 20 minutes since the metal is melted straight inside cold chamber machines the machine, which makes it perfect for high-volume manufacture.
The hot chamber approach, however, is best suited for lower melting point metals like these:
- Lead alloys
- Zinc alloys
- Magnesium alloys
Melted metal is driven into the die cavity via the gooseneck’s plunger mechanism during the process. The plunger retracts, the mould opens, and the final casting is taken out when the metal sets inside the die. The cycle then runs again as the plunger drives fresh molten metal into the die cavity while the mould closes.
The fast, accurate, consistent hot chamber process is hailed. Moreover it guarantees better corrosion resistance and longer die life.
Cold Chamber Die Casting
Though it uses the hot chamber sand casting technique in one important way—the metal is not melted inside the casting machine—cold chamber die casting is different.
Rather, metal is melted outside in a high-temperature furnace and molten aluminum is then ladled to the cold chamber die casting machine. The molten metal then is driven into the die cavity by a hydraulic piston.
Higher melting point metals like aluminum alloy these would find this process perfect:
- Copper
- Magnesium
- Aluminium and their respective alloys
Magnesium alloys, for instance, can reach temperatures up to 650°C (1,200°F) and start melting at about 360°C (680°F). Because of their higher melting points, some magnesium alloys need the cold chamber process even if some may still use the hot chamber approach.
For manufacturing parts needing more strength, durability, and hardness—that is, for demanding industrial uses—cold chamber die casting is especially successful.
Materials Used in Die Casting Dies

Die casting aluminum die casting performance and durability mostly rely on the construction materials used. Typical supplies consist of:
1. H13 Steel
- Renowned for remarkable durability and thermal resistance.
- Perfect for die casting processes in high-temperature surroundings.
2. P20 Steel
- reasonably priced, reasonably durable material.
- Designed for low-volume, simpler manufacturing operations.
3. Copper-Based Alloys
- great heat conductivity for quicker cycles of cooling.
- Often found in uses needing exact temperature control.
4. Tool Steels (H21, H11)
- Provides exceptional wear resistance and hardness.
- Often used in settings with high pressure die casting.
Design Process for Die Casting Dies
Designing successful aluminum die casting dies requires many important processes to guarantee durability and accuracy.
Step 1: Conceptual Design
- Specify the intended material properties, geometry, and part dimensions.
- Create thorough 3D models to see die features and possible obstacles.
Step 2: Material Selection
- Select suitable die materials for mechanical stress and thermal fatigue resistance.
Step 3: Cavity and Gate Design
- To guarantee seamless molten metal flow, specify gate locations, flow channels, and venting points.
- Good design improves part quality and lessens air entrapment.
Step 4: Cooling System Integration
- Use effective cooling channels to speed cycle times and control die temperature.
Step 5: Prototype Testing
- Run sample manufacture to find possible design flaws or defects.
- Change the die construction as necessary for better performance.
Die Casting Process Using Dies
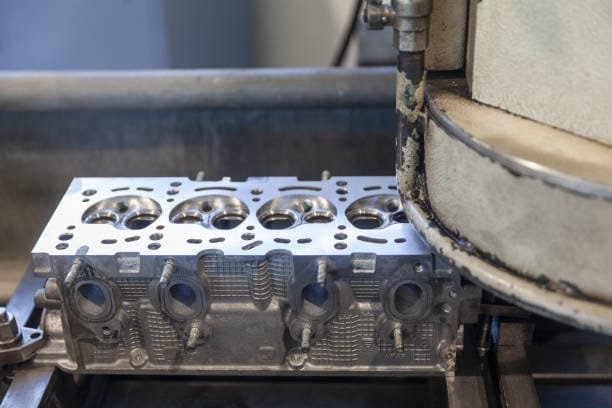
To produce excellent metal parts, the aluminum die casting process itself consists in a sequence of exact actions. These actions comprise:
1. Preparation
- The die is preheated to avoid thermal shock.
- To enable part ejection and lower wear, a die release agent is sprayed on.
2. Injection
- To shape the die cavity, molten metal is injected under high pressure.
3. Solidification
- The molten metal takes the intended form quickly cooling and solidifying within the mold.
4. Ejection
- Once set, the part is removed from the mold either automatically or with ejector pins.
5. Trimming and Finishing
- Extra material is cut off, and finishing techniques including coating or polishing are applied.
Common Defects in Die Casting Dies
Defects in die casting dies can arise even with exact engineering. Knowing these problems facilitates the execution of remedial actions.
1. Porosity
- brought on during the injection process by trapped gas or air.
- Correct pressure changes and venting will help to solve this problem.
2. Cracks and Wear
- Die cracks can result from prolonged use or too strong thermal stress.
- Frequent inspection and repair help to extend die life die cast aluminum parts.
3. Incomplete Fill
- Results from molten metal failing to totally occupy the cavity.
- This can be fixed by guaranteeing enough pressure and changing gate design.
4. Flash Formation
- Flash defects arise from too much molten metal escaping the die cavity.
- Enhanced clamping pressure can help to avoid flash-related flaws.
Maintenance and Care of Die Casting Dies
Extending die life and guarantees best performance depend on proper maintenance die cast aluminum partsdie cast aluminum parts. Important customs include:
Regular Cleaning
- Eliminating die release agents, metal residue, and trash increases die efficiency.
Inspection and Repair
- Regular inspections for surface flaws, cracks, or misalignment help stop expensive repairs.
Lubrication
- Lubricating moving parts lowers friction and stops wear.
Temperature Management
- Steer clear of rapid temperature swings to lower thermal fatigue and extend die life molten metal fills.
Industry Applications of Die Casting Dies

Die casting dies find extensive application in many different sectors, including:
- Automotive: Manufacturing engine parts, transmission cases, and wheels is automotive.
- Aerospace: Aerospace: Developing strong yet light aircraft parts.
- Electronics: Creating exact homes for tools and appliances.
- Medical Equipment: Forming robust surgical tools and devices is medical equipment die casting manufacturer.
Advantages of Die Casting Dies
Many advantages of die casting dies help to enhance manufacturing techniques:
- High Precision: High precision guarantees very low dimensional variation in parts.
- Fast Production: Encouragement of high volume, low cycle times manufacturing helps die halves
- Versatility: Makes manufacturing possible with magnesium, zinc, and aluminum among other metals.
- Durability: Withstanding repeated high heat and pressure is durability.
Challenges in Using Die Casting Dies
Die casting dies can provide some difficulties even if they are efficient:
- High Initial Costs: Development of custom dies can be costly initially.
- Complex Design Process: Calls for advanced knowledge for detailed designs.
- Maintenance Demands: Perfect performance depends on regular maintenance, thus maintenance demands.
Conclusion
Modern manufacturing depends on die casting dies as essential tools since they help to produce exact and durable metal components. Manufacturers can maximize efficiency, reduce flaws, and extend die casting mold part lifetime by knowing the kinds, tools, materials, design approaches, and maintenance techniques. Industries looking for highly accurate, high-performance components depend on investing in quality die casting dies.