Find out the ins and outs of plastic molding prices, such as the injecting molding cost factors and cost analysis, how an optimized injecting molding cost can be achieved and the ideas of professionals on the method to minimize incurred costs to manufacture while quality is maintained.
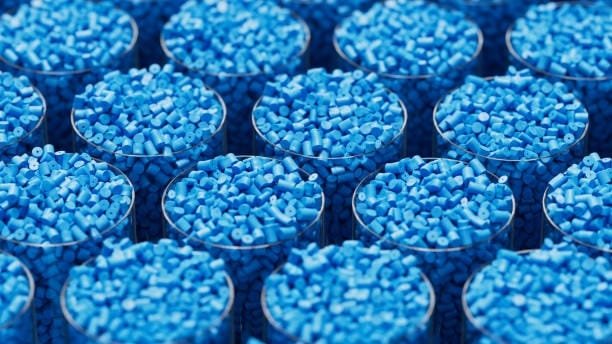
Plastic molding, particularly the injection molding process, is one of the most effective, most versatile as well as cost effective manufacturing processes in the production of high quantity of plastic parts in industries. Compared to other factors that affect the manufacturing cost, it is important that manufacturers, product designers, and business owners find it essential to understand the complex factors that comprise the manufacturing cost of plastic molding as a means of streamlining its cost and staying within expected quality levels. This resource will take you through all the details related to the cost of plastic molding, including the initial tooling costs, per-unit costs of production, and everything in between, so you could make decisions in regards to your manufacturing projects.
Understanding Plastic Molding Cost Fundamentals

The costs of plastic molding include various elements that have effects on the overall cost of manufacturing plastic pieces by utilizing distinct molding operations. The major cost factors would be tooling and mold design, mold material cost, labor cost, machine running charges and post processing needs. These expenses are quite different according to the complexity of the product, the volume of production, the material quality and specifications. Knowledge of such basic cost elements will enable manufacturers to estimate project budgets more traditionally and find some ways to optimize the costs without outmoding the quality of the products or the quality of its functionality self mating parts.
Types of Plastic Molding Processes and Their Cost Implications

The various plastic molding techniques involve different costing and cost-effective factors, especially for injection molded parts . Most common is injection molding, which has large tooling investment needed, with low per-unit costs at high volumes. The blow molding technique is superior in hollow items whose tooling is moderate and easily expandable. The method of rotational molding offers economical answers to the big hollow parts that use minimal tooling costs. Thermoforming is highly cost effective on thin walled component and packaging. Compression molding is a process suitable to thermoset materials that have a moderate cost of tooling. Every process has the optimum volume ranges and part geometries that optimize the cost benefit and process selection becomes an essential factor in the project economics.
Injection Molding Cost Breakdown and Analysis
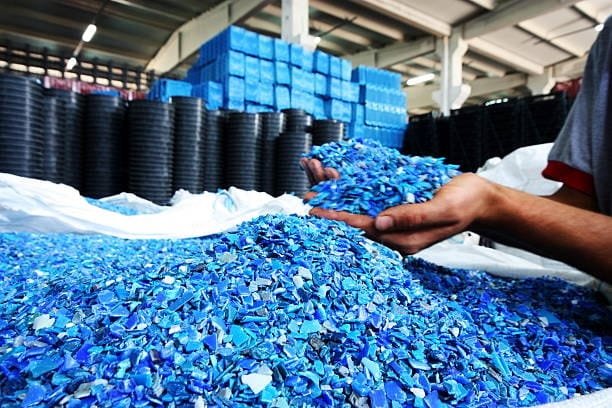
The costs of using injection molds comprise some major elements that shape up economics of a project. The tooling cost is usually the biggest up front investment with simple molds costing roughly $5,000 and complex multi cavity tools capable of high production costing in excess of $100,000. Prices of the materials depend on the resin type and range between 1-3 dollars per pound of commodity plastics and 10-20 dollars per pound of engineering plastics. The cost of machine time, including setup costs, varies with the cycle time, the size of machine and the local labour rates usually 30-100/hour. The setting expenses relate to the fixing of molds, preparation of materials and verification of quality. Finishing processes such as assembly, decoration or packaging are more expenses. The break down helps in good estimation of the costs and finding out areas of optimization.
Material Selection Impact on Molding Costs
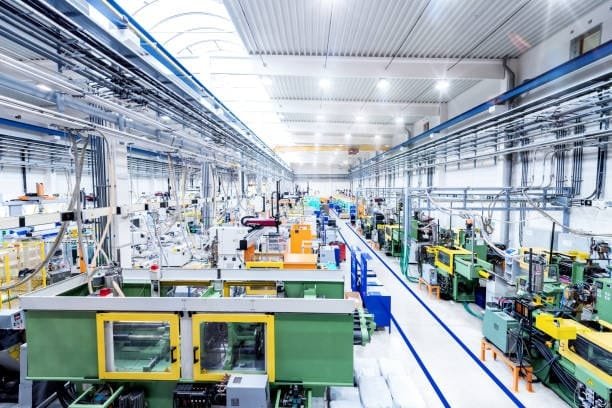
The choice of materials has a great contribution to direct material and processing costs involved in plastic molding. Lowest material costs commodities, such as polyethylene and polypropylene, can be commodity plastics that possibly involve design tradeoffs. The engineering plastics such as ABS, polycarbonate and nylon offer superior properties with modest escalation in prices. Demanding applications are made to be possible by high-performance materials that are priced highly, such as PEEK, PPS, and liquid crystal polymers. A secondary consequence of material selection is influence on processing conditions, cycle times, and on mold wear resulting in indirect cost implications. There are cost and sustainability issues, which are presented by recycled and bio-based materials. This is the secret of balancing material properties, cost and processing need in order to attain optimal total cost of ownership on some applications.
Tooling and Mold Design Cost Factors

Tooling is the other key cost factor in plastic molding project and a lot of parameters affect the cost of molds. The complexity of the parts will lead to the tooling cost of intricate geometrics, undercuts, tight tolerances in the constant need of fancy mold stances. The number of cavities has an impact on the cost, multi-cavity molds cost more initially but the same cost reduces due to high volume. The choice of material used to make molds has an influence on cost and durability, with aluminum used to make prototypes, and hardened steel being used in volumes. The various requirements necessary in the surface finish, the complexity of the cooling and automation system costs involved enhance productivity. Quality validation functions, ejection systems and gate design are aspects that lead to the total tooling investment. Knowledge of these factors can best serve to design for mold production to be efficiently produced at an acceptable rate as required by performance.
Volume-Based Cost Scaling in Plastic Molding
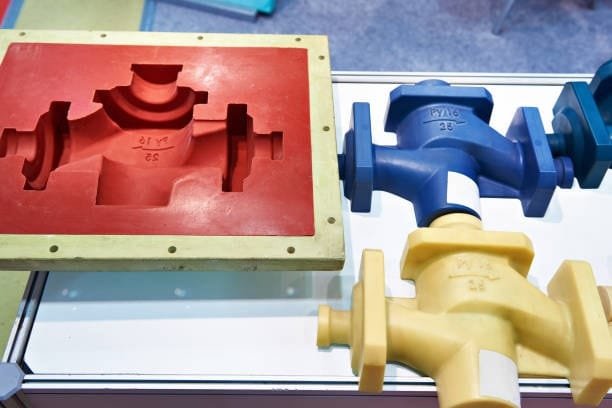
The level of production volatility has severe impacts on the economics of plastic molding in terms of fixed cost amortization and economy of scale. Small lot production will distribute the high cost of tooling over a smaller number of parts, which increases the individual cost of production. Medium volumes start attaining cost efficiency because tooling costs are shared in a more favourable manner. The benefits of mass production are maximized because the costs due to the full use of tooling, maximized cycle time and buying in mass are utilized. Extremely large quantities might warrant such cost-saving items as multi-cavity molds or automated operations. Familiarity with the volume breakpoints assists in setting the best production policies and pricing patterns. Predictability of volume is important in making the right tooling investments and the realization of expected cost.
Labor and Overhead Cost Considerations

Labor and overhead are important parts of plastic molding costs and they have a lot of geographical differentiations and differences in facility capabilities. Direct labor involves machine operator, quality inspectors, and material handlers, where rates range between 15-50 dollars per hour across the world. Indirect labor Lower Structure Indirect labor includes engineering, maintenance and administrative support. Facility overhead comprises of building expenses cost, utilities, insurance and depreciation of equipment. There is a strong variation in cost due to geography and cost of manufacturing varies 3-5x among regions. The degree of automation in molding equipment fluences the labour requirements where highly automated facilities decrease direct labour and raise the equipment cost. Knowledge of area level cost structures can aid in optimal location decisions of the manufacturing operation and cost advantage.
Quality Requirements and Cost Implications
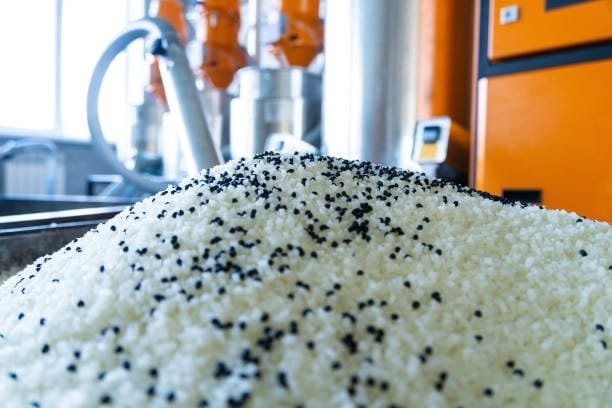
The grade specifications also have a big influence on the expense of plastic molding in terms of material selection, procedure check, and validation. Ordinary commercial fine quality normally needs crude dimensional control and visual inspection. The automotive quality standards require improving process control, statistical process control and a lot of documentation. The quality of medical devices needs to be validated procedures, traceability of materials, and regulatory observation, which also affect the cost of injection . The aerospace quality standards are the most demanding to accommodate and validate fully the processes with certification requirements. When the level of quality is higher, material costs are higher, cycle time is increased, special equipment is necessary and significant testing is required. The need to find a balance between quality requirements and cost limitation take some time to consider the needs of applications and the risk tolerance.
Geographic Location Impact on Molding Costs
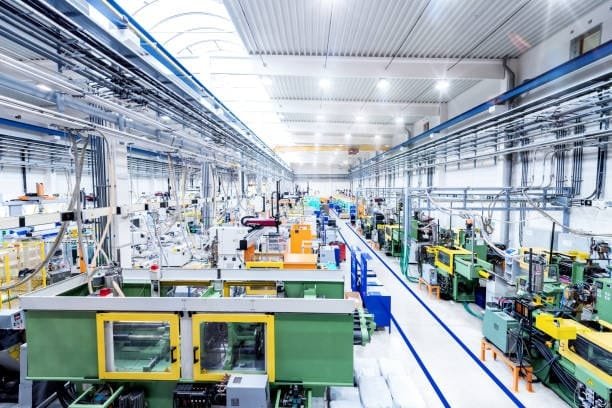
With the significant impact of the manufacturing location in the costs of plastic molding in terms of labor rates, availability of material, the cost of energy and the plethora of requirements of regulations. Compared to Asian manufacturing centers, labor prices are America-competitive, although there might be more lead time and communication problems involved. North American plants offer closeness benefits and quality uniformity at elevated costs of labor. European production unites the high quality perfection as well as the medium cost surcharges. Emerging markets are cost-effective, although they can be quality and infrastructure related problems. Total landed costs are influenced by transportation costs, custom duties and fluctuations in the exchange rates. The strength of intellectual property remedies, quality checks and supply chain dependability differ as one region to another. The potential to be achieved in manufacturing decision making by means of comprehensive cost based location analysis involves all the factors of costs.
Secondary Operations and Finishing Costs

Plastic molded parts have secondary operations which are valuable yet expensive. Labor, fixtures and quality control are also required to assemble its operations, which adds 10 cents to 2 dollars per part based on the level of complexity. Processes used in decorations such as painting, printing or pad printing are between $0.05 and 0.50 per part depending on need and complexity of coverage. Adding controlled features requires machining operations that are expensive in critical features. The services of welding, bonding and joining are special and need specialized equipment and skills. Still, the services, such as packaging and labeling, are of additional convenience with the presence of related overheads. Testing and validation services are quality-assuring but lead time and costs are increased. The knowledge about secondary operation issues assists to reduce total cost of manufacturing and value deliver.
Design for Manufacturing Cost Optimization
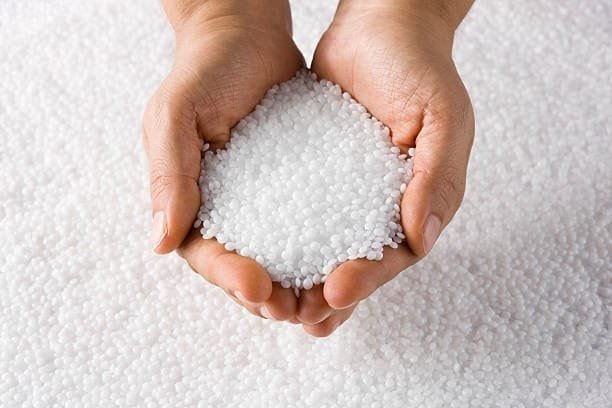
Design optimization is the best technique to have an affordable price as far as plastic molding options are made and functional. Complexity in mould, which poses several difficulties in manufacturing, is minimized by simplifying the part geometry. Design modifications that eliminate the use of undercuts eliminate the requirement of intricate mechanisms of the molds. Optimization of wall thickness will provide a proper filling and also reduce material consumption and cycle time. It is possible to design multi-cavity molding and reduce the cost of volume. Adding draft angles helps get parts out of the mold easily and less wear on the mold. Economies of scale are achieved by having the product lines share common features and materials. Design collaboration between the engineers and the manufacturers in the early days saves the cost of molding since the low cost benefits of the tooling investment are found. Proper design review techniques guarantee low costs of solutions without losing out on performance.
Prototyping and Low-Volume Production Costs

The costing of the low-volume production and prototyping is different as compared with high-volume production. Ink jet, stereolithographic and other rapid prototyping techniques such as 3D printing present rapid and low cost assessment of a design design, albeit in limited materials. Soft tooling in aluminum or rapid tooling steels can provide a part that is production in nature at a lower investment tooling cost. Bridge tooling: interim tooling Bridge tooling is used to provide intermediate solutions when production tooling is being developed. Access to low-volume production process without the ownership of tools is available in the form of low–volume injection molding service. Both methods have the breakpoints of the volumes at which other alternatives are more cost-efficient. Knowledge of prototyping economics enables one to optimize development schedules, spending and flexibility of the design and its verification needs.
Long-Term Cost Considerations and Tool Life
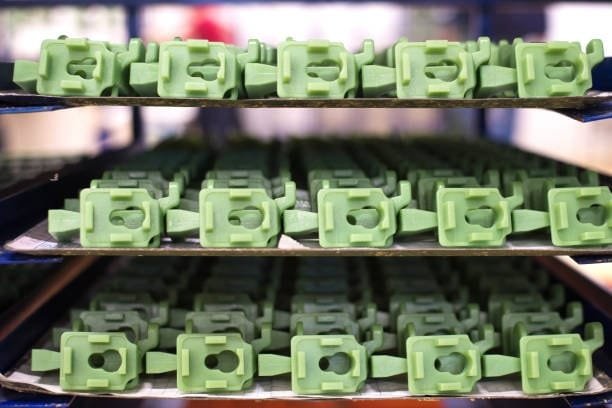
Long term cost planning involves knowledge of life of molds, maintenance and replacement patterns. Depending on the materials and design, the production tooling release between 500,000 to several million of parts. The costs of maintaining a mold used to be cleaning, repairing and substituting a component amounting to 5-15 per cent of the value of annual production. There are design modifications or process improvement costs incurred through tool adjustments. There should be planning and allocation of funds to maintain production concerning the process of end-of-life tool replacement. Preventive maintenance programs increase the life of tools and minimize those that fail unexpectedly. With appreciation of the total cost of ownership throughout product life cycles, precise financial estimates and decision making processes can be arrived at concerning tooling investment/maintenance policies.
Cost Estimation Methods and Tools

Plastic molding projects demand structured methods as well as suitable tools when estimating the cost. Parametric estimating is fast in predicting cost based on the characteristics of parts as well as history. Detailed bottom-up estimating treats every element of costs in an attempt to check the accuracy. Quotes through vendors offer market level prices to meet a particular need. Design Alternatives can be analyzed at high speed using cost modeling software. Estimates are reality checked by benchmarking with comparable projects. Constant cost monitoring and performance helps enhance estimating efficiency in the future. Creation of internal cost databases will increase estimation and competitive positioning abilities. Estimation of costs is implemented in systematic processes which lower financial risks and allow developing competitive pricing strategies.
Comparing Plastic Molding Costs to Alternative Manufacturing

Knowledge of cost of molding plastics compare to other manufacturing processes aids in streamlining a production decision. Machining is flexible and precise but expensive per-unit on complex geometries. 3D printing has the benefits of increasing design freedom and fast production speed but with speed and material constraints. Die casting will have outstanding surface finish and existence of thin walls and necessitates varied tooling investments. Stamping is particularly suitable to thin, flat items, and not three-dimensional. Building as a collection of many parts offers flexibility, at the price of labour and inventory costs. The processes also possess optimal utilization areas according to geometrical, volumetric, material and economical needs. Comparison of processes thoroughly guarantees the best decisions in the manufacturing process.
Automation Impact on Molding Costs

Information technology used in automation has tremendous impacts on the cost structures of the plastic molding because of labor savings, quality augmentation, and productivity advancements. The simple automation involves ejection of parts and conveying systems which has moderate investment with acceptable returns. High levels of automation involve the use of robots in dealing with parts being handled, inspecting quality and packaging at higher costs but high labor savings. Lights-out manufacturing allows production with no staff, with a maximum reduction of labor costs, but demands rather complex systems. Automation makes variable costs decrease but also increases the fixed cost changing the volume breakeven calculations. Automation makes quality improvements which cut costs of scrap and rework. As automation economics enhances efficient decisions, so does it position and enhance competition within the diverse market segments.
Supply Chain and Logistics Cost Factors

A portion of the total costs of plastic molding that is not commonly considered in the set of total expenses in the field is supply chain and logistics prices. The costs on transportation of raw materials by suppliers may influence the costs of the material especially specialty resins. Depending on weight, volume and destination, finished goods are shipped to the customers. Shipping goods internationally entails custom fees, paper work and longer transit periods. Stock carrying costs involve storage cost, insurance and working capital requirements. Supply chain interruptions introduce the expediting cost as well as the delay of production. Shoring could help in minimizing transportation expenses but restrict supply materials. End-to-end analysis of cost of supply chains will guarantee the best sourcing and supply chains strategies so as to retain the service levels and cost competitiveness.
We are aware of the intricacies of worldwide supply chain in management of plastic molding processes at GWT Worldwide. Being professional logistics service provider that major in global freight forwarding and supply chain related solution, we can assist manufacturers to optimize logistics cost by offering comprehensive services of air freight, sea freight, China Europe railway transport and Amazon FBA shipping assistance. We have mastered the art of customs clearing and warehousing; thus we can ensure a hustle-free international presence and our well-developed technology in logistic offers visibility and efficiency across the supply chain.
Market Trends Affecting Molding Costs

Market trends in force today greatly determine the cost of plastic molding and the expectation on the upcoming prices. Fluctuation in raw material prices influence material prices and planning demands. It helps to raise wages and implement automation through labor shortage in the manufacturing areas. Material to be recycled and environmental compliance are extra costs as demanded by sustainability. Regulatory developments affect the approvals of materials and process validation requirements. New opportunities of cost optimization are due to technological advances in processing equipment and automation. Possible disruption of supply chains influences the availability of materials and the stability of prices. Knowing market trends will help to manage cost proactively and plan strategically towards the variation in the economy and competitions.
Sustainability and Environmental Cost Impacts

Plastic molding is subjected to environmental considerations that affect the cost by way of cost of materials, efficiency of the process, and compliance to regulations. Recycled products are usually expensive as compared to virgin resins but are sustainable in nature. Bio based plastics have higher prices but are eco-friendly electrical discharge machining. The processing equipment used is energy-efficient; the cost of operation as well as carbon footprint is much less. Reductions of wastes limit expenditures on materials and waste disposal. Environmental compliances need monitoring, reporting and possible remediating expenses mold size. Considerations of life cycle assessment influence the selection of materials and process methodology. The reduction of carbon footprint can cost in the short run and give competitive advantages in the long run. It is crucial to analyze the balance between sustainability and cost objectives as it needs detail-planning and understanding.
Risk Management and Cost Contingencies
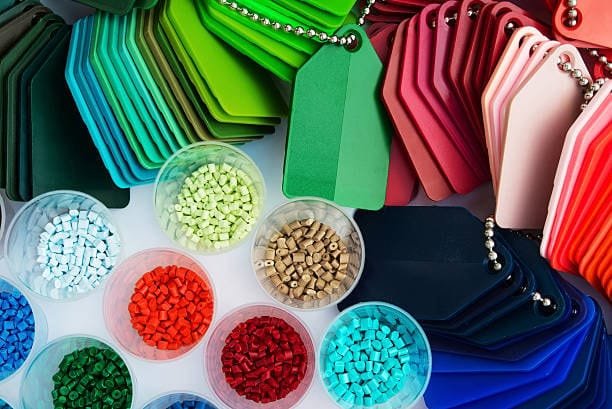
The risk management methods enable one to safeguard against cost upshots in the plastic molding projects. Fluctuation of material prices necessitates swings hedging or flexible pricing plans. Supply chain risks require backup suppliers as well as buffer stock. The problem of quality may cause delayed costs and rework. Failure of equipment entails maintenance contingencies and back up plans. Tooling alteration costs are incurred as a result of design change in the production. Process updates and revalidation costs might be necessary as a result of regulatory changes. Risk assessment determines the possible cost exposures as well as strategy mitigation plans. Proper contingency planning safeguards budgets of projects as well as delivery and quality constraints.
Technology Advances and Future Cost Trends
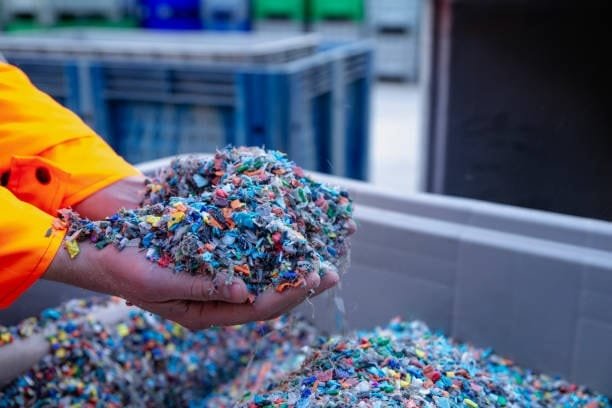
The new technologies are likely to have a drastic change in cost and potentials of plastic molding later. Developed materials will provide improved characteristics, albeit they will be expensive in the short-term. Digital manufacturing processes facilitate cost reduced customization in mass. The parameters of the processes are optimized and the waste is minimized with artificial intelligence and machine learning. The incorporation of the industry 4.0 gives the ability to monitor in real-time and predictability of repair. Integration of the additive manufacturing results in hybrid solutions to production. The environmental cost and compliance are lower with the utilization of a sustainable processing technology understanding injection molding cost. Wood and laser wastes keep improving because of the drastic change of technology. A good knowledge of the trend in technology will be able to strategize on future costs and advantages in competition in the changing markets.
Cost Benchmarking and Competitive Analysis

The frequent cost benchmarking will help in maintaining the competitive position and also finding areas of improvement in plastic molding operations family mold. The data obtained in industry cost surveys, including how much does injection molding cost injection molding machines, is the market comparison data on different processes and different regions injection molding material. Analysis of competitors shows how the competitors are pricing their products and on positioning complex molds
. Internal benchmarking monitors trends and improvement in costs over the periods of time cnc machining. Identification of best practices brings out effective cost cutting strategies reduce injection molding costs. Supplier benchmarking makes the material and service prices competitive injection molding expensive. Periodic reviews of cost keep in focus any change in market and possibilities of optimization. The strategic consideration and continuous improvement depend on the systematic benchmarking processes to gain sustained competitive advantage injection mold tooling.
Conclusion
The subject of plastic molding cost constitutes an outstanding variation of material and tooling, processing, and the market cost that makes extensive background study necessary to manage such projects effectively cost of injection molding. The secret to optimization of costs, including obtaining an injection molding quote, is early design partnership, methodical evaluation of cost and strategic choices of all cost elements. Volume planning, process selection and/or geographic considerations can have tremendous effect on overall economics of a project and its competitive levels aluminum molds.
The achievement of cost management is to be balanced between the short term costs pressure and long term strategic aims, such as, quality requirement, sustainability goals and market position insert molding. The development of technology and the trends in the market form challenges and opportunities in terms of cost-saving, forcing individuals to learn and change on an ongoing basis plastic injection molding process.